-
Homepage
-
Sealing knowledge
- Sealing Materials, and Elastomers: An Overview
Sealing Materials, and Elastomers: An Overview
Elastomers as sealing materials constitute various materials for specific seals and applications in sealing technology. Elastomers are dimensionally stable and elastically deformable plastics. A prime example is rubber bands. They are dimensionally stable yet possess elastic properties and tensile stress with an entropic effect (entropy elasticity). Similar to thermosets, elastomers are interconnected through covalent bonds between individual molecular chains (macromolecules). This rubber elasticity occurs as the tangled polymer chains respond to tensile stress by stretching or untangling. Also see our materials for seals and gaskets.
Seals are an indispensable part of our lives. Without them, there would be no running water, no power plants, and no cars. Given the diverse possible applications for seals, there are numerous materials for seals, each coming with many advantages and some disadvantages. Therefore, at Kofler - Dichtungen, we also offer special seals and custom-made seals and gaskets. As a manufacturer of seals, you will find in our section an overview of the most important sealing materials, their advantages and disadvantages, and their optimal applications.
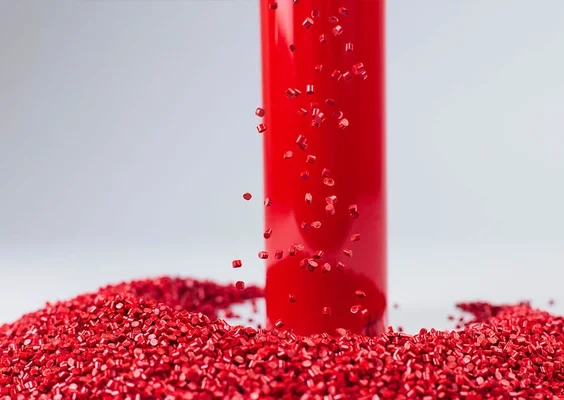
Working materials - What are the advantages of different sealing materials?
The possible areas of application and requirement profiles for seals and their different materials or sealing materials are numerous:
flat gaskets and seals for aqueous goods to be transported, oils or gases; profile seals made of silicone, for example, must withstand many deformations elastically every day in door frames, dynamic seals in hydraulic cylinder systems (e.g. piston seals, rod seals) must withstand high pressures, temperatures, and the various hydraulic media. (Also read – What are hydraulic seals?)
That is why many different materials are used as sealing material. Thus, the optimal material can be advantageously used for practically every field of application, while the disadvantages are not significant.
Elastomer - The most important sealing materials at a glance
Today, there are numerous materials (Wikipedia - elastomer, elastomers) that can be used as sealing material. Thanks to modern manufacturing processes, the properties can even be fine-tuned within a material class.
The main elastomer materials for seals and gaskets are:
These thermoplastic elastomers are also frequently used:
- HPU: hydrolysis-resistant polyurethane
- HPU solid: a harder HPU for special applications
- HPU MOS2: a compound of HPU and molybdenum sulfide
“Thermoplastic” means that these materials can be softened and reshaped in the heat (e.g. pressing). For example, elastomers are also used as substitutes for natural corks in wine bottles.
The following thermoplastics are also very suitable for sealing technology:
- POM: Polyoxymethylene
- PTFE: Polytetrafluoroethylene (Teflon)
- PEEK: Polyetheretherketone
Now we will show you the advantages and disadvantages of these materials and where they can be used.
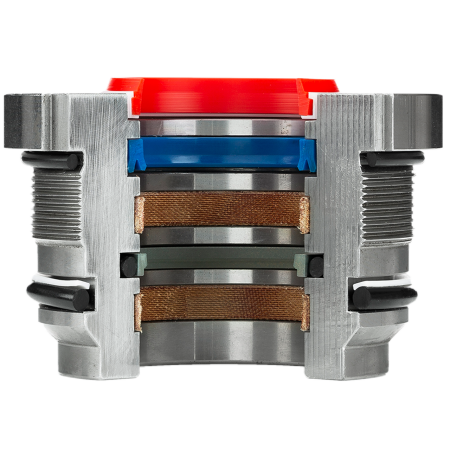
Get in touch with us!
We perform best under pressure! Personalized advice for the highest demands and a fast delivery guarantee ensure your satisfaction. Contact our sealing experts.
We look forward to your inquiry."
NBR Gaskets and Seals - Acrylonitrile Butadiene Rubber
NBR stands for Nitrile Butadiene Rubber. It is synthesized through a chemical reaction between acrylonitrile and butadiene, followed by either thermal or chemical vulcanization.
NBR seals and gaskets exhibit exceptional mechanical resistance. Depending on the content of nitrile, NBR is compatible to a good or very good degree with low-aromatic hydrocarbons, oils, and fats. This makes it an ideal choice for fuel lines and seals that come into contact with oil, such as hydraulic seals, radial shaft seals, and Simmerring seals.
NBR has moderate stability against hot acids and bases.
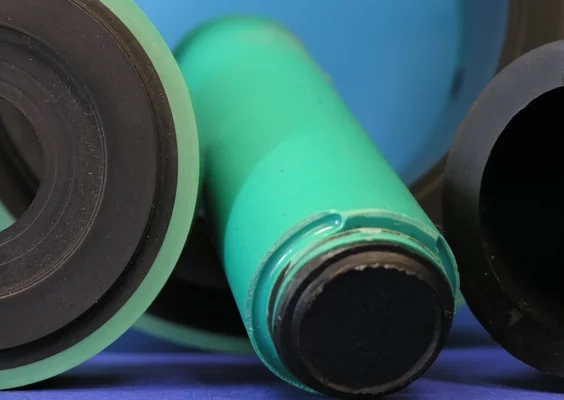
Viton® seals, FKM, FPM
Unfortunately, there are often uncertainties with fluoroelastomers, as the names have changed. FKM is the designation for fluoroelastomers according to the US standard ASTM. The abbreviation FPM was used in DIN/ISO. Viton® is the trade name of a fluoroelastomer from DuPont. Generally, FKM is produced from fluorocarbons with subsequent crosslinking (similar to vulcanization).
FKM is very resistant to aggressive chemicals, mineral oil, gasoline, diesel, alcohol, and withstands high temperatures. FKM has a significantly higher density than other elastomer materials.
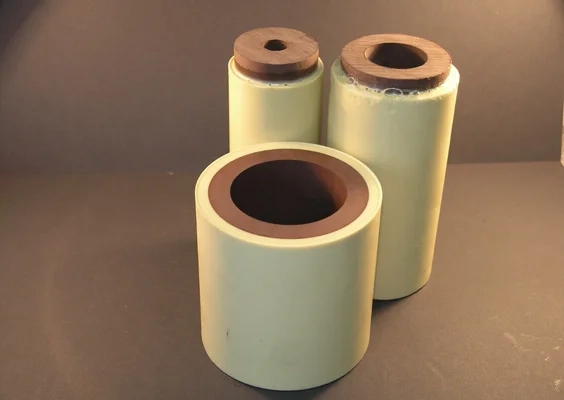
EPDM Seals and Gasket - Ethylene Propylene Diene Rubber
The abbreviation EPDM stands for ethylene propylene diene monomer rubber. In general, a distinction is made between natural rubber and synthetic rubber. EPDM is a synthetic rubber, i.e. an artificial rubber. This rubber technology is produced by the chemical reaction of three components, with subsequent vulcanization. Additives such as carbon, calcium carbonate or pigments are used in the production to ensure the fine adjustment of the material properties and the colour.
Due to its chemical nature, EPDM is very stable to polar substances such as water or alcohols such as glycol, acid, alkali, heat, UV radiation and remains soft and elastic up to -40°C (-40°F). EPDM is poorly compatible with non-polar substances such as mineral oil, petrol, diesel, kerosene and halogen-containing solvents.
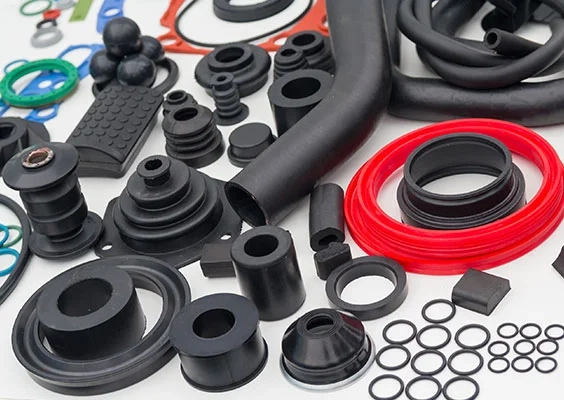
Silicone seals: WMD/VMQ
Silicone rubber, colloquially known as "silicone," is created through crosslinking reactions from specific silicone oils, a process very similar to vulcanization. There are various manufacturing methods classified according to the number of components and the application temperature.
The most well-known technique involves one-component crosslinking at room temperature, commonly used in standard household silicone sealants. For sealing technology, especially for applications such as O-rings, high-performance materials are often produced using a more complex process with multiple components at elevated temperatures.
Silicone seals are particularly utilized where performance at low or high temperatures (under -50°C up to 200°C or -58°F up to 392°F) is needed, including excellent electrical insulation properties, ozone resistance, and UV radiation resistance. Additionally, silicone as a material is physiologically safe, making it suitable for medical applications and food processing.
However, silicone is incompatible with acids, alkalis, oils, and fuels. It is also not suitable for mechanical stresses
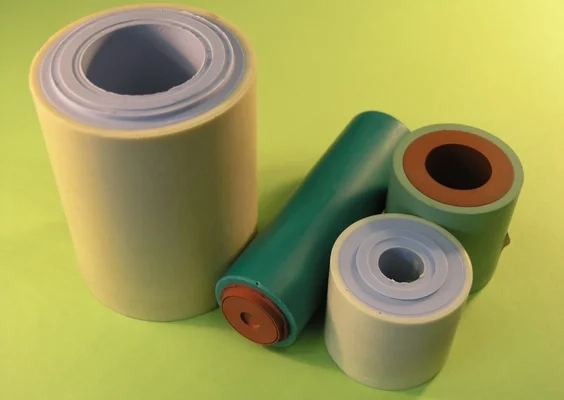
FFKM Seals and Gasket – Perfluoroelastomer
FFKM seals and gaskets consist of perfluoroelastomers, which have an even higher fluorine content than FKM. It is made from at least three raw materials: tetrafluoroethylene (raw material for PTFE (Teflon)production), a perfluoro ether (improves elasticity) and a cross-linkable component that allows final vulcanization. FFKM is therefore like elastic Teflon.
FFKM is an absolute high-performance material that can fully exploit its advantages in extreme conditions. It can withstand aggressive chemicals and oxygen plasma and is suitable for continuous use above 300°C (572°F). The production of seals and gaskets from FFKM is expensive, so this material is only used in high-tech systems, or if a seal defect would be associated with very high costs and damage.
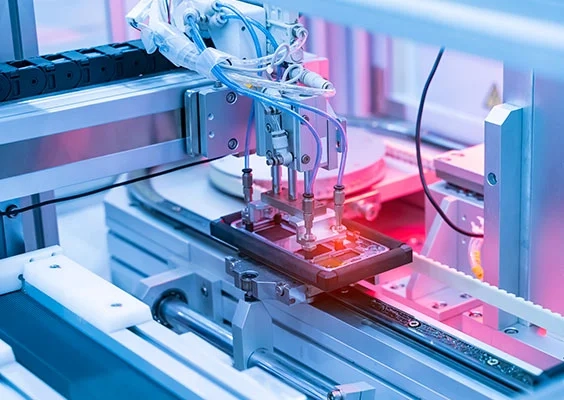
HPU, HPU solid and HPU-MOS2
HPU stands for hydrolysis-resistant polyurethane, a thermoplastic material capable of being deformed and processed at high temperatures. This material exhibits particularly advantageous mechanical properties, boasting high elasticity alongside impressive wear and abrasion resistance.
HPU’s chemical resistance is also noteworthy, suitable for use with fats, mineral oils, hydraulic fluids based on mineral oil (though caution with additives is advised), and aliphatic hydrocarbons like propane, butane, and fuels, including gasoline, diesel, and kerosene. Additionally, HPU withstands dilute acids and bases, seawater, and water up to 90°C (194°F).
It can also work with HFA and HFB group pressure fluids. However, HPU is not resistant to aromatic solvents such as benzene and toluene, chlorinated hydrocarbons (such as dichloromethane, chloroform, trichloroethylene), ketones, glycols, glycol-based brake fluids, as well as concentrated acids, bases, amines, and hot water over 100°C (212°F), which can deteriorate it.
HPU Solid is a special formulation that offers greater hardness and can withstand pressures up to 400 bars (5801,51 PSI). It displays the same media resistances as standard HPU, but features enhanced wear and abrasion resistance. This formulation is particularly beneficial for applications where PTFE, normally chosen for its sliding properties, is not feasible due to complex installation or other mechanical stresses.
HPU-MOS2 is a composite material combining HPU with MOS2, marrying HPU's mechanical benefits with the lubricity of MOS2. This blend, thanks to its improved sliding characteristics, is especially suited for pneumatic applications. Kofler - Dichtungen offers a variety of pneumatic seals in different sealing materials, including HPU-MOS2.
The remarkable attributes of HPU position it as the optimal and most commonly utilized material in manufacturing hydraulic seals, such as rod seals, piston seals, and wipers. Furthermore, a wide range of HPU mixtures exists, some softer or tailored for low-temperature applications. We invite you to consult with our seal experts for more information on these custom solutions.
PTFE: Polytetrafluoroethylene, Teflon
Polytetrafluoroethylene, widely known as "Teflon," is an extremely versatile material. Its unique chemical composition makes it a distinctive type of plastic.
Teflon is utilized specifically when high self-lubrication and chemical resistance are demanded. It lacks any adhesive qualities and boasts very low friction values. Another notable feature is that static and dynamic friction are equal, allowing it to start moving or stop without jerking.
Its chemical resistance spans almost all chemicals, including hydraulic fluids, acids, alkalis, and hot water, and it is non-flammable. PTFE is particularly prevalent in the food industry due to its inert nature, ensuring it does not transfer to the processed goods.
However, Teflon is relatively sensitive to mechanical stresses such as lateral forces and compression.
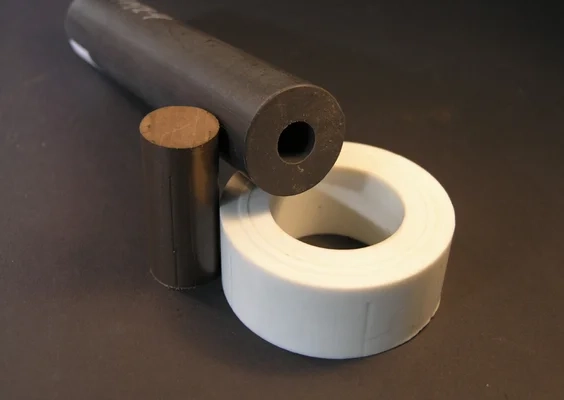
Areas of application of the different sealing materials
The application areas of the different sealing materials are very broad, from fuel technology to alcohol-based hydraulic fluids to food processing. Since all materials have different advantages and disadvantages, there is a separate material for practically every application.
For example, some seals swell on contact with fuels and become brittle, others are attacked by alkalis or wear quickly under mechanical load and force. In this section you will learn which sealing materials are suitable for your application.
Oil-Resistant Sealing Materials
Oil-resistant sealing materials must retain their elasticity when in contact with oils, greases and hydrocarbons and must not swell. NBR seals (e.g. Perbunan) and Teflon or FKM are ideally suited for such applications. In the case of mechanical stress, seals with a fabric insert or so-called compounds with glass fibres, bronze or carbon are used.
Fuel Resistant Sealing Materials
Fuel-resistant sealing materials largely coincide with oil-resistant materials: NBR, Teflon and FKM. However, mineral oil processing also uses aromatic-rich raw materials and fuels such as petrol and diesel are much more volatile and combustible, so that special material qualities are used. These ensure special tightness, fuel resistance and load capacity.
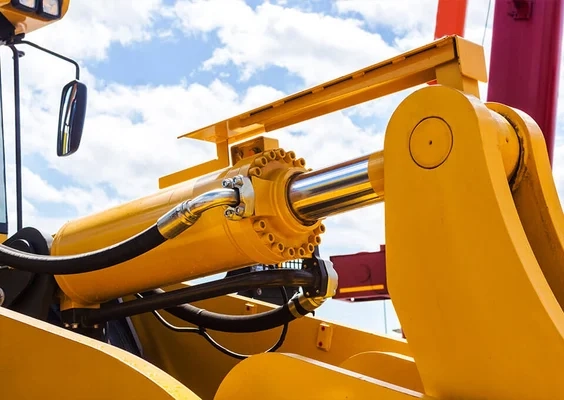
Sealing Material for the Food Industry
The modern food industry also requires seals in its equipment, for example, in the bottling of mineral water and fruit juices. These seals often need to withstand rotations and rotational movements.
Moreover, the highest standards of health safety and food-grade quality are demanded, which are also regulated by authorities. Many materials are available in food-grade versions. These include, for example, NBR, EPDM, FKM, or PU, which are often manufactured in special colors specifically for the food and pharmaceutical industries. Silicone and PTFE are generally considered suitable for food applications
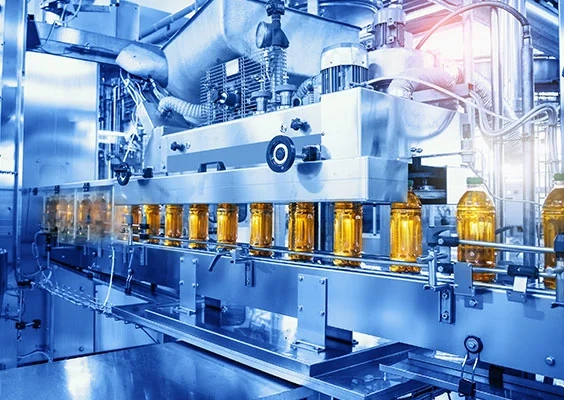
Weather-resistant sealing materials
Seals are utilized not just indoors, but also outdoors. In such environments, they are exposed not only to process media or the materials being transported but also need to endure abrasive dust, wind, rain, ozone, air, temperature fluctuations, and UV light.
Silicone, EPDM, Teflon, and FKM have been established as sealing materials resistant to weather conditions.
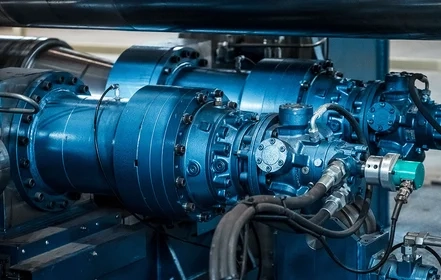
Heat-resistant sealing materials
Many industries operate high-temperature plants in which an increased ambient temperature is to be expected (e.g. metal processing) or process heated raw materials (chemical industry). This fact must also be taken into account when choosing sealing materials, as costly sealing defects must be avoided.
Silicone, PTFE and FKM are particularly heat-resistant, but also graphite and mica materials in flat gasket technology. The specific selection must be made taking into account the other requirements (mechanical stress, pressure, resistance to oils, acids, alkalis)

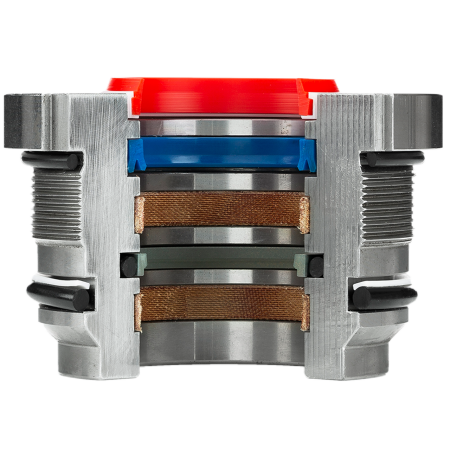
Get in touch with us!
We perform best under pressure! Personalized advice for the highest demands and a fast delivery guarantee ensure your satisfaction. Contact our sealing experts.
We look forward to your inquiry."
High Pressure Sealing Materials
Industrial seals require the highest performance under extreme conditions. Particularly in power plants, industrial plants, and mechanical engineering, there are often significant demands on mechanical and thermal load capacity during constantly recurring load changes.
High-performance materials and composite materials (so-called compounds) are used here. Examples include HPU solid, PTFE (Teflon) compounds with bronze or carbon, composite silicones, and NBR with fabric inserts.
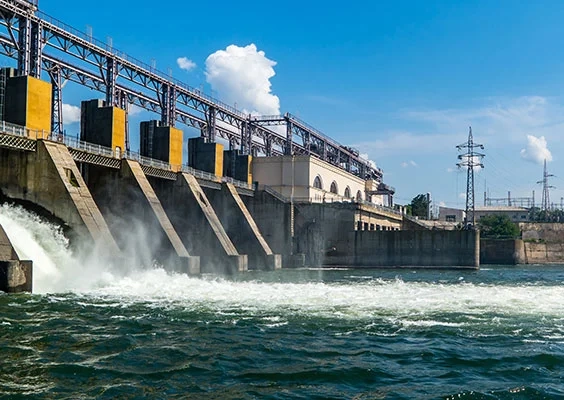
Wear protection of seals
Seals often face stringent requirements regarding tightness and chemical resistance. When also subjected to high mechanical loads, it's essential to use wear-resistant materials or develop multi-component seals.
In such designs, the component resistant to wear absorbs mechanical forces, thereby protecting the other component. Polyurethane (PU) is especially wear-resistant, making it ideal for situations of increased friction or when minimal lubrication is possible. In these scenarios, PTFE or PU MOS2 are the preferred materials owing to their low friction properties.
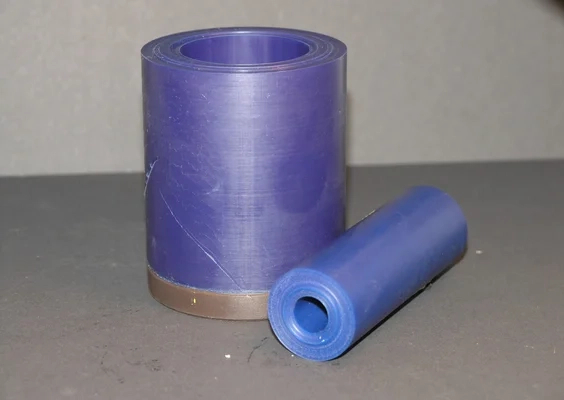
Other sealing materials
Entirely different materials and unique forms are utilized in flat sealing technology. Aramid fibers (such as Frenzelit® Novapress or Klinger® Klinger-Sil) have proven to be reliable and are frequently used. In extreme temperature environments where standard plastics (like polyethylene) would degrade, materials such as graphite and mica are chosen. These substances are exceptionally well-suited for high-temperature applications.
Conversely, traditional materials like pressed cork, leather, and wool felt primarily hold historical significance in sealing applications. The initial radial shaft seals were crafted from leather in a metal frame. This design has since been supplanted by seals made of rubber or PTFE. These historical materials are mainly utilized for support and vibration damping.