-
Homepage
-
Sealing knowledge
- Sealing Technology – All about Seals and Gaskets
Sealing Technology – Everything about Seals and Gaskets
If you require a comprehensive overview of seals and sealing technology, our seal knowledge section is exactly what you need.
Initially, we will explain the functions of seals and gaskets and the various types available. We will then highlight some applications for seals, ranging from flat gaskets to hydraulic seals and pneumatic seals, including their applications.
You will learn about the elastomer materials used as seal materials and the modern manufacturing processes most commonly applied in seal production. Subsequently, we clarify the high standards set for premium-quality seals.
In conclusion, we will demonstrate how to correctly store your seals to ensure they remain operational over many years.
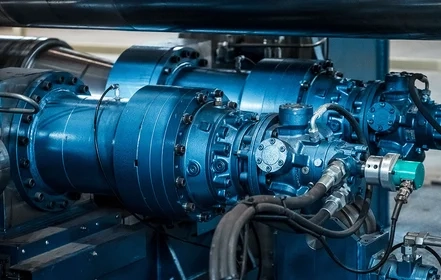
What exactly is the function of a seal?
Seals generally serve the purpose of partitioning two spatial areas to either slow down or completely halt the transfer of solid materials, liquids, or gases. A straightforward example is the flat gasket used in flange connections of piping systems, which prevents both the escape of the conveyed material and the ingress of air and moisture.
Depending on the nature of the conveyed material, the seal is a safety-critical component. If toxic or corrosive liquids or gases are being conveyed, a faulty seal could pose a danger to both personnel and the operating plant.
Depending on its specific implementation, sealing technology also facilitates the frictionless and wear-resistant movement between two components, such as the hydraulic seal found between the cylinder and piston or piston rod. For demanding applications, a sealing set composed of several matched components is employed. What exactly is a hydraulic seal?
Static and dynamic seals
Seals are divided into static and dynamic seal types.
Static seals are located between two immovable sealing surfaces. They have continuous contact with the surfaces to be sealed and can therefore have very low leakage rates. Static seals can be relatively easily manufactured and easily installed and maintained, such as a rubber sealing ring in a water connection.
Dynamic seals have the demanding task of sealing between two mutually movable sealing surfaces. In this case, a small sealing gap is unavoidable and, as a result, a certain leakage rate is always to be expected.
This sealing gap can be advantageously utilized in many applications, since lubricants can be introduced into the sealing gap during operation. This increases maintenance intervals as friction and wear can be reduced.
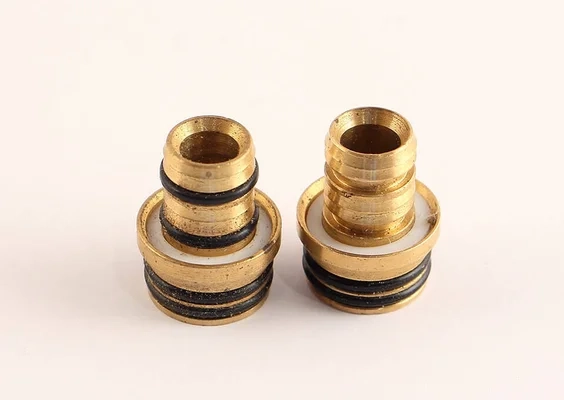
Why are seals and gaskets so important?
Seals and gaskets perform numerous important tasks that are essential for the functioning of machines and technical systems.
On the one hand, seals protect the machines from environmental influences. They prevent the penetration of moisture, dirt, dust, or metal chips into the housing, where they would have a harmful effect and would significantly shorten maintenance intervals.
On the other hand, seals prevent the leakage of materials from the inside of a machine or conveyed goods from pipes into the environment. This is particularly relevant when dealing with environmentally harmful substances, such as hydraulic fluid from a machine or toxic or corrosive liquids or gases from an industrial plant.
In addition, seals and gaskets can be essential for the operation of a machine. A hydraulic system would not function without a piston seal or rod seal and moving metal components would immediately wear out upon direct contact.
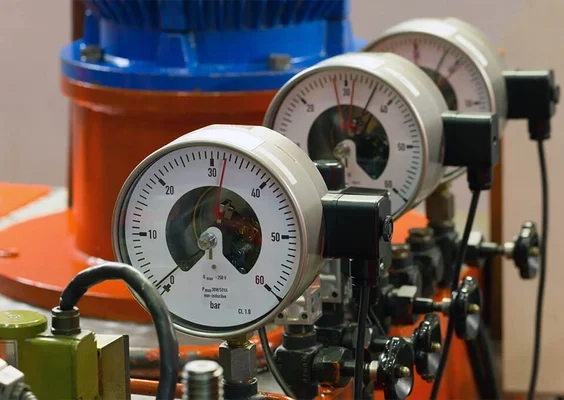
What sealing materials are available?
Numerous high-performance sealing materials such as elastomer materials have been developed to cover a wide range of applications with their individual requirements. The spectrum of material properties in terms of hardness, elasticity, chemical resistance, operating temperature, electrical insulation properties and much more has become very large.
For virtually any application, the ideal material can be selected from several options, e.g. PU, NBR or PTFE compounds for piston seals for hydraulic cylinders.
The following sealing materials are often used:
- PU Gaskets (Polyurethane)
- NBR seals (Nitrile Butadiene Rubber)
- PTFE and PTFE compound gaskets (PTFE with carbon, bronze, or MoS2 addition)
- EPDM gaskets
- Silicone gaskets
- Viton gaskets
- Seals made of special materials, such as peek, Kalrez ®, Aflas ®
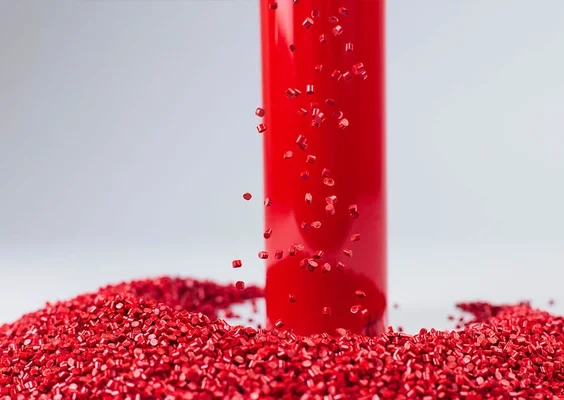
Where are seals gaskets used?
Seals and gaskets are utilized wherever it is necessary to prevent the escape of materials and/or to minimize leaks at the sealing surfaces of moving parts. This applies across practically all industrial sectors.
In every production facility, hydraulic or pneumatic devices are employed for the filling or packaging of goods, devices that would not operate without hydraulic or pneumatic seals.
Even in domestic settings, pipe or hose connections are found with sealing elements that prevent leakage. Every motor vehicle requires seals too, for example, piston seals in the engine or within the braking system.
Modern machinery also relies on seals, such as shaft seals (simmering seals), which are used between the housing and a rotating shaft, and can also be found between the dip tube and standpipe of a mountain bike suspension, as an example.
As we can see, seals are practically indispensable across a wide array of applications, and without them, many conveniences and necessities of our daily lives would not be possible.
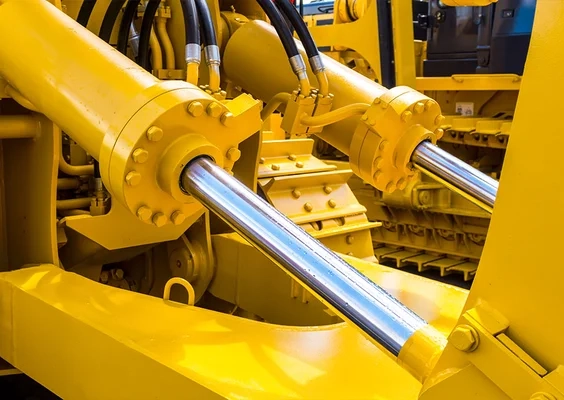
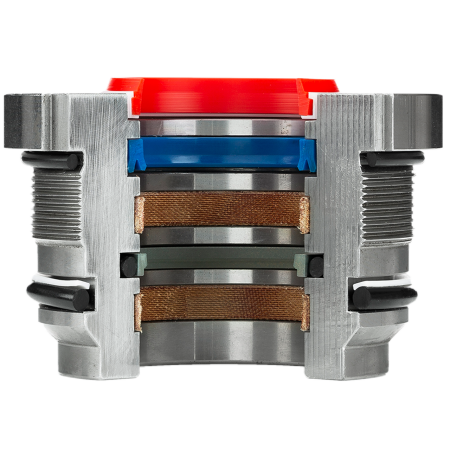
Get in touch with us!
We perform best under pressure! Personalized advice for the highest demands and a fast delivery guarantee ensure your satisfaction. Contact our sealing experts.
We look forward to your inquiry."
How are seals manufactured?
Seals are manufactured in established, automatable processes whose parameters such as pressure, temperature, processing speed can be controlled within very narrow limits. This ensures a consistently high quality in production and reproducible goods.
One of the following procedures is usually used:
- Punching seals from flat sealing material.
- Injection moulding for large series of small seals
- Extrusion for profile seals
- Water jet technology
- CNC - milled or turned profile seals
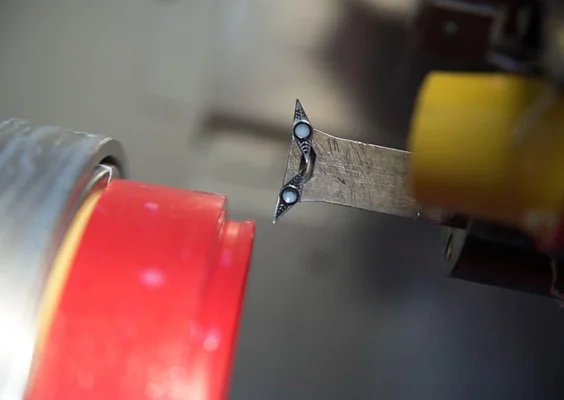
What requirements should a high-quality seal guarantee?
High-quality industrial seals must meet the highest standards. Even standard seals must be precisely manufactured and meet their specifications within narrow limits.
In general, high tightness or low leakage rates are required and are essential in particular for special seals that are used in environmental and safety-related applications.
Seals must be low-maintenance with a long service life. In addition, the installation or replacement should be as simple as possible.
The different application areas of seals and gaskets
- Engine Technology
- Mechanical Engineering
- Automotive Industry
- Conveying Processes
- Material Transport
- Chemical and Pharmaceutical Industry
- Process Engineering
- Dosing and Filling Plants
- Food Industry
- Plant Construction
- Power Plants
- Energy Sector
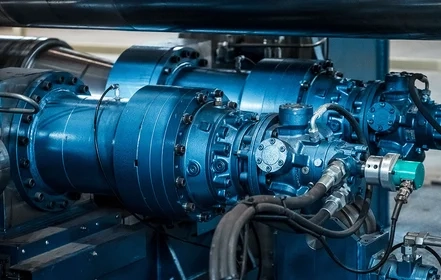
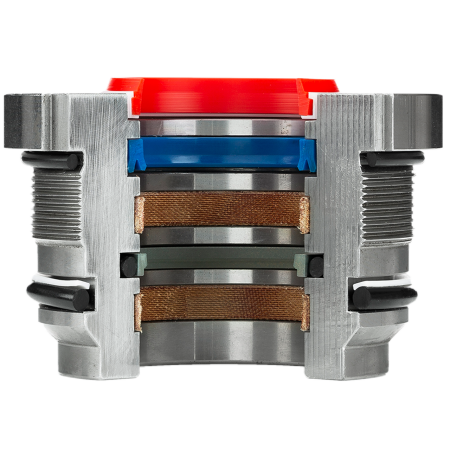
Get in touch with us!
We perform best under pressure! Personalized advice for the highest demands and a fast delivery guarantee ensure your satisfaction. Contact our sealing experts.
We look forward to your inquiry."
Storage of seals and gaskets
The storage of seals plays a crucial role in their performance. Properly stored, seals and gaskets can remain operational for several years. Poor storage conditions, however, can significantly shorten their lifespan or cause them to lose functionality even before they are installed.
So, what constitutes proper storage? Generally, seals should be kept at moderate temperatures, that is, between room temperature and just above the freezing point (5 to 20 °C or 41 to 68 °F).
Ideally, seals should be stored in an airtight manner. This helps to prevent the ingress of abrasive dust and dirt. Additionally, protection against UV light and ozone is important, as these elements can severely damage seal materials. They can quickly degrade the materials' properties, leading to embrittlement and cracks.
Seals and gaskets must be stored free from external forces, meaning without any pressure or deformation acting on them (for example, from being under heavy objects). Otherwise, the seals may become permanently deformed.
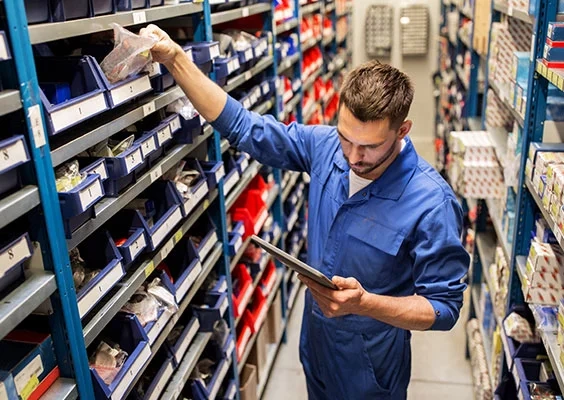